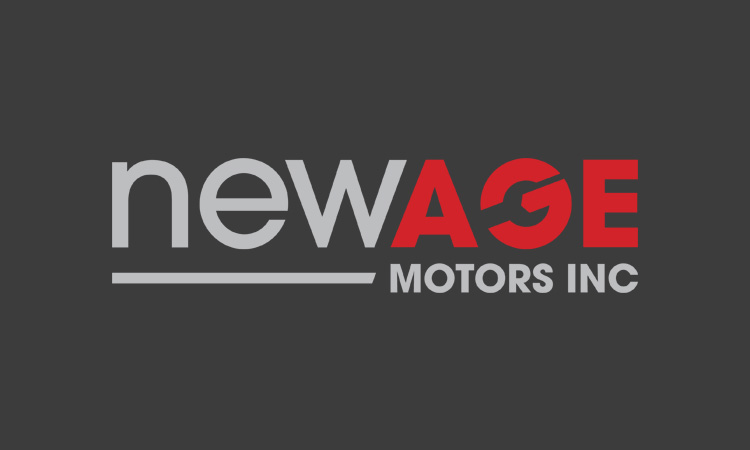
Why Heavy Truck Brakes Need Regular Inspections for Safety and Savings
Key Takeaways
-
Heavy truck brake systems rely on important components like pneumatic chambers, springs and slack adjusters. These highly engineered systems, including brake drums, chambers and air compressors, ensure the safest, most effective performance. Knowing how these components interact is key to regular maintenance and ensuring driver safety.
-
Heavy truck air brake systems fundamentally depend on compressed air to engage a vehicle’s brakes. This technology offers outstanding robustness and energy efficiency, making it perfect for a heavy-duty application. For this to happen, it’s important that normal air pressure is maintained.
-
Regular brake inspections can save costly repairs down the line, improve safety on the highways, and keep our truckers compliant with industry regulations. Routine inspections can spot wear, leaks or other signs of misalignment before they lead to a serious incident.
-
Managing friction and heat through quality brake linings and proper maintenance prevents brake fade and ensures consistent performance under heavy loads.
-
Advanced technologies such as ABS, EBS, and brake monitoring systems increase braking efficiency, lower stopping distances, and aid in preventive maintenance. Keep an eye on these innovations to improve the safety of our roadways.
-
Driver training on proper braking techniques and early problem detection plays a critical role in reducing brake wear, preventing accidents, and extending the lifespan of braking systems.
Heavy truck brakes are of escalating importance to safety and performance of the great behemoths of the highways. These braking systems are certainly designed to stop big, fat trucks. They rely on complex systems, including air brakes and hydraulic brake systems, to deliver consistent decelerating force.
Specifically, they are designed to quickly stop massive vehicles, usually over 30,000 kilograms, and do so with efficiency, even under severe, continuous usage. Proper maintenance of these systems, including regular inspections and timely replacement of brake pads or discs, is essential for optimal operation.
Knowing how heavy truck brakes work and what they need to consistently perform at their best will get you on the road to improving safety and minimizing downtime. Let’s take a look at their parts, advantages, and maintenance best practices to get your rig running like a top.
Understand Heavy Truck Brake Systems
Heavy truck brake systems are complicated but critically important components that directly impact safety. They’re built to work hard in the vehicles that haul our heavy, essential freight. These systems operate under the premise that a series of mechanical components, emissions-producing compressed air, and friction materials must all work in concert.
Understanding their components, operation, and control function will ensure more productive preventive maintenance, safer operation, and much more.
Key Brake System Components
Heavy truck brake systems are made up of numerous parts camshafts, slack adjusters, air reservoirs, etc. Each part performs a distinct function. Camshafts change rotational motion of the wheels into linear force, pushing brake shoes against the drum.
Slack adjusters keep just the right distance between brake shoes and drum, guaranteeing reliable braking force. Air reservoirs hold the compressed air produced by the onboard compressor, usually keeping pressure at a standard 689 to 827 kPa (100–120 psi).
Other components such as brake chambers and drums convert air pressure into mechanical force, stopping the large vehicle quickly and efficiently. This interaction underscores the need for routine inspection, because failure of any one component can affect proper function of the whole system.
How Air Brakes Operate
Air brakes work by using compressed air provided by an engine-driven compressor. When you depress the brake pedal, the air pressure acts to the triple-valve system, which regulates brake application and release.
Unlike hydraulic brakes, air brakes fail in a safe “on” position, applying brakes if pressure drops too low, such as during a system leak. Inadequate performance Maintenance is usually an issue. Smooth, consistent performance is vital for stopping trucks up to 36,287 kg (80,000 pounds).
Managing Friction and Heat
Friction materials do their part in stopping brake fade by being able to resist high extreme heat conditions. Heat, which is produced during brake application, can be detrimental to performance if left uncontrolled.
High-quality linings and/or advanced materials such as ceramics help to improve heat resistance.
Material |
Heat Resistance |
Durability |
---|---|---|
Organic |
Moderate |
Average |
Semi-Metallic |
High |
High |
Ceramic |
Very High |
Very High |
Why Routine Brake Inspections Matter
For heavy trucks in particular, the braking system is a key component to their safety, regulatory compliance, and cost of operations. By getting in front of brake issues with routine brake inspections, you’ll stabilize the long-term performance of your vehicle. They’re not just good for business; they help keep everyone on the road safe.
By making routine inspections a top priority, you’ll not just be safeguarding your investment, but preventing dangerous accidents, costly repairs and compliance violations.
Prevent Costly Future Repairs
Ignoring brakes will ultimately result in costly repairs, including loss of life. Ignoring early warning signs like uneven brake pad wear or strange noises can result in catastrophic failure. You may find yourself wearing down your rotors or calipers and that repair can be very costly.
You can catch small problems, like worn brake pads or low brake fluid before they become bigger and more expensive on their own. Performing simple routines such as replacing pads is overall more cost effective than the repair of ruined drum systems or hydraulic lines. Preventable brake issues such as air leaks or overheated parts can result in brake repairs of up to $20,000.
Signs needing immediate inspection:
-
Grinding or squealing noises
-
Vibrations while braking
-
Uneven pad wear
-
Reduced braking power
Ensure Road Safety Compliance
Brake inspections shouldn’t be a cost consideration—they should be a road safety consideration. Every day, regulations such as the Basic Inspection of Terminals (BIT) and Department of Transportation (DOT) standards require routine inspections.
Failure to comply can result in costly fines, liability concerns, or vehicular crashes themselves. With appropriate brake function, the risks are reduced, and both drivers and the public are better protected. Keeping abreast of the legal baseline helps to hold us all accountable to higher duty without compromising safety.
Meet Regulatory Requirements
That’s where certified mechanics, like those in the Navy’s maintenance training program, come in to improve compliance. Establishing a paper trail for inspections protects transit agencies during audits or litigation as legal evidence.
Safety Regulatory entities such as DOT focus on intense maintenance practices to make sure that vehicle brake systems are held to high safety standards. Following these guidelines will not only save you money, but protect your fleet’s and your reputation.
Common Heavy Truck Brake Problems
Heavy truck brake systems are under a lot of stress from the weight and duty cycle requirements of these vehicles. Being mindful of these common brake problems can go a long way to ensure safety, efficiency, and reliability out on the road.
Identify Soft or Spongy Braking
-
Soft or spongy brake pedal A soft or spongy brake pedal is usually a sign of air in the brake lines, or a low brake fluid level. All of these problems can cause loss of hydraulic pressure needed to stop the vehicle.
Air leaks in brake chambers, for example, can prevent the effective conversion of air pressure into mechanical force. Worn push rods further exacerbate the problem. Diagnosing soft braking begins with checking the fluid reservoir for signs of leaks or contamination.
Testing brake chambers and making sure air lines and valves are working properly can avoid bigger issues down the line.
Troubleshooting Tips:
-
Check and refill brake fluid.
-
Inspect air lines for leaks.
-
Bleed the brake system to remove trapped air.
Address Vehicle Pulling Issues
If your truck begins to pull to one side when you brake, this likely indicates a serious issue. Usually uneven brake wear or unbalanced brake drums are the culprits.
Brake shoes meant to wear in uniformly can get out of square after many miles, leading to wobble and shake. Replacing brake shoes in pairs keeps performance even.
Paying attention to steering feedback when braking can catch the early stages of pulling long before it’s noticeable.
Diagnose Unusual Brake Noises
Squealing or grinding sounds may be a sign of worn brake pads, which should be replaced every 80,000 km on average. Warped rotors or unbalanced drums can cause these noises to occur.
Maintaining a record of sounds gives mechanics useful information to diagnose what you are experiencing.
Investigate Vibrations
Brake vibration is usually caused by warped rotors due to hot spots, or more commonly uneven wear. Early detection through regular inspections ensures optimal brake performance, minimizes risk, and avoids emergency repair costs.
How to Inspect Heavy Truck Brakes
Keeping brakes properly inspected and maintained is key to safety and performance of heavy trucks. That’s why a systematic approach for finding these potential problems before they become dangerous is key. Consider this comprehensive guide your blueprint for performing a more thorough brake inspection.
Check Air Compressor and Reservoirs
The compressor creates the pressurized air needed for the truck to brake. Begin the inspection process by looking at the compressor, looking for signs of physical damage and air leaks.
There shouldn’t be any cracks and any valves or petcocks should seal well, with no leaks that would reduce air pressure. Keeping air pressure at manufacturer-specified levels is key.
Too low or too high pressure can significantly lower braking power. With an easy, regular check of the compressor and reservoirs, you can ensure consistent performance and avoid unwanted surprises with a failure.
Inspect Brake Chambers
Brake chambers use air pressure to produce mechanical force, which serves to apply the brakes. Determine the size of the chamber by noting the square-inch area of the diaphragm—sizes vary from 6 to 36.
Check for signs of wear, corrosion, and physical damage. Watch the sealing, because the wrong sealing will cause air to leak in.
Signs that brakes need repair include hissing sounds, braking that is uneven and visible cracks. Consult manufacturer specifications to measure pushrod stroke and be sure it’s within the limits for adjustment.
Evaluate Slack Adjusters
Slack adjusters keep the proper brake adjustment for safe maneuverability. Look for free-stroke pushrod distances greater than 19 millimeters, which indicates the brake is out of adjustment.
Most new-style pushrods feature indicator markings to make this task easier. Always adjust slack to manufacturer specifications and have a routine check to ensure that there is no brake failure before it happens.
Examine Drums, Shoes, and Linings
Ensure drums and shoes are not worn or cracked. Check lining wear. Linings should be at least the thickness required by your local jurisdiction for minimum safety standards.
Worn or warped linings can increase stopping distances. Proper maintenance goes a long way, including the regular cleaning of components, especially after harsh winters, and routinely replacing worn parts.
Ensure Heavy Truck Brake Safety
Keeping heavy trucks brake safety is key to avoiding accidents and keeping our economy rolling. A strong, proactive approach is needed, considering that braking systems represent the highest category of out-of-service violations at 25.2%. This highlights the need for frequent brake inspection, driver vigilant pre-trip awareness, and organized operational safety procedures.
1. Monitor Air Pressure Levels
Correct air pressure is essential to brake performance. Low air pressure is a leading cause of brake failure. This problem puts at risk the ability to brake a vehicle that can weigh upwards of 80,000 pounds.
Frequent inspections, using a quality air pressure gauge, will ensure that tires are properly inflated. Tools like digital pressure gauges, air compressors and leak detectors are vital monitoring tools.
2. Adjust Slack as Needed
Slack adjusters maintain proper brake force by automatically adjusting slack to keep the ideal clearance between the brake shoes and the drum. When slack is misadjusted, it can drastically decrease braking force and increase stopping distance.
Drivers need to adhere to manufacturer calibration instructions for slack adjusters, including periodic recalibration and necessary adjustments to prevent overt wear or slack adjuster failure.
3. Replace Worn Components Promptly
Timely replacement of part of safety parts like brake pads, drums, and linings is essential. Delayed replacements can lead to Brake Fade, which has classic warnings such as slow vehicle takeoff.
A systematic checklist of commonly worn components helps make sure every part is inspected and nothing is missed.
4. Check for Leaks Regularly
Should a truck with air leaks bring its weakening braking efficiency. Check fittings, hoses and valves regularly and fix any leaks immediately.
Without this, the system will fail, and braking will not be trusted.
5. Keep Brakes Clean and Maintained
Dirt has a drastic effect on brake performance. Use brushes, air blowers, and non-corrosive cleaners to avoid damaging components during cleaning.
Regular maintenance not only prolongs its life, but guarantees it will be used safely.
6. Schedule Professional Inspections
Only certified brake experts can find problematic issues that are otherwise hidden. Routine inspections always give a wealth of knowledge and reinforce performance for all brakes.
Advanced Brake Safety Technologies
Today’s heavy trucks brake systems, while still heavy-duty and complex, are much safer and more reliable than their predecessors. These advancements are propelled by the desire to create superior braking performance for vehicles upwards of 80,000 lbs (36,287 kilograms).
Automatic braking and air disc brakes (ADBs) can help tremendously in crash prevention. Discussions centered around the important contribution they make to preventing thousands of deadly accidents and injuries each year. For example, ADBs can bring a fully loaded truck to a stop within 68.58 meters, showing their increased stopping capability.
EMB (Electric Master Cylinder) embedding the systems’ components, which feature electric parking brakes, lowers complexity while increasing long-term durability. These innovations prevent injury and save lives. In addition, they minimize costly legal exposure, including nuclear verdicts that can reach over $13 million per case.
Anti-lock Braking Systems (ABS)
ABS prevents wheel lock-up in cases of panic braking, allowing for more control and stability. This technology is key to making heavy vehicles safer, particularly in slick roadway conditions.
By maintaining steady steering and braking, ABS reduces the likelihood of skidding and vehicle rollovers. Keeping these systems in good repair is not only common sense, it is a safety imperative. Key features include:
-
Real-time wheel speed monitoring
-
Adaptive braking pressure adjustments
-
Enhanced maneuverability and stopping precision
Electronic Braking Systems (EBS)
EBS combines electronic controls with air brake technology for quicker, more responsive, and energy-efficient braking. These systems help provide shorter stopping distances and better overall response times, both critical for urban operation as well as highway grade crossing situations.
Fleet managers enjoy less wear and better safety, which lead to savings over the long term.
Brake Monitoring Systems Explained
Moreover, brake monitoring systems are able to deliver real-time data about the status of an agency’s brakes, facilitating preventive maintenance. Additional benefits include less downtime and longer component life.
Features often include:
-
Wear level sensors
-
Temperature monitoring
-
Diagnostic alerts
Factors Affecting Brake Wear
Realizing a full range of factors at play, leading to accelerated brake wear in HDT, is crucial to maintaining performance and safety. Actual brake longevity would depend on several factors, from environmental conditions to variations in load and even driving habits. All of these factors greatly influence the rate at which braking components wear.
Impact of Environmental Conditions
Climate and environmental factors, including weather conditions, terrain, and road attributes, have a significant impact on brake wear. For one, if winter conditions are icy, the increased need to brake frequently and often with more force is hard on brake pads and shoes. Unsurprisingly, driving through additional wet or muddy conditions threatens your braking materials.
This moisture can cause corrosion and loss of efficiency. Extreme heat during the summer months can result in brake components overheating, resulting in component material breakdown. To cope, consistent maintenance that focuses on these unique circumstances is imperative.
For example, lubrication and ensuring that no rust or grit has gotten into the brake components are especially important in humid months. Environmental factors such as steep mountain inclines, regular stopping in urban environments, or roads laden with debris put additional stress on a brake system.
-
7 Snow and ice
-
Fallen trees from strong winds, heavy rain or flooding
-
Factors that promote brake wear
-
Overheating
-
Ambient brake dust on a vehicle parked on a dusty or gravel road.
-
Effects of Load Variations
How much weight a truck hauls has an enormous effect on how well the vehicle has to brake. Increased weight loads require more braking force, leading to the generation of additional heat through friction. Overloaded vehicles—commercial vehicles in particular—are a big part of the problem, increasing wear and increasing the risk of failure and safety hazards.
Aligning brake performance with the respective load is important, but it is important to follow weight limits to avoid overload conditions. Ceramic brake pads perform great with heavier loads and can last up to 112,000 km. In comparison, organic pads typically wear down after only 32,000 km.
Influence of Driving Habits
Aggressive driving habits like hard braking and rapid acceleration not only waste fuel, they put extra wear and tear on brakes. Smooth, gradual braking and avoiding unnecessary speeding is far better. Thorough driver training can help promote more progressive driving habits, both increasing brake life and enhancing fuel efficiency.
-
Stop naked braking suddenly or hard on the brakes in a hurry.
-
Maintain safe following distances.
-
Avoid excessive use of brakes on downhill grades.
Driver Training and Brake Performance
Driver training is critical to maximizing brake performance for all heavy trucks. Quality instruction ensures that drivers are equipped with the understanding required to best operate air brake systems. This driver training helps them accomplish smooth, consistent stops once again, including with the best-in-class 80,000-pound load.
Sequential braking made possible by the triple-valve principle—one of the main characteristics of air brakes—provides the fine control required. Ninety percent of heavy-duty trucks are relying on air brakes. Getting the most out of these systems is critical to keep our transportation system safe and efficient.
Proper Braking Techniques
Threshold braking is an essential skill for all drivers, as it delivers maximum braking effort without wheel lockup. In short, anticipating stops is just as important. Doing so can lessen wear on brake components and can enhance fuel efficiency.
Maintaining consistent pedal force through the entire stop helps improve pad wear and stop control. Drivers can follow these techniques for efficient braking:
-
Apply gradual pressure to avoid sudden stops.
-
Use engine brakes on steep grades to reduce strain.
-
Monitor trailer alignment during braking to maintain stability.
Early Problem Detection Skills
Identifying potential brake problems before they become dangerous hazards is not only smarter, it’s safer. Effective training prepares drivers to recognize indicators such as loss of braking power, strange sounds, or increased pedal length.
When issues are reported quickly, it helps everyone by encouraging a proactive culture of safety first. Regular inspections, like checking air storage tanks, valves, and lines for wear, make sure reliability is built into each model as well.
Understanding System Limitations
Drivers need to know the limits of the brakes and this is especially important when excessive speed, overloaded weight, or adverse road conditions are a factor.
Driver training and brake performance misconceptions, like a false sense of quick stopping power, have contributed to tragic crashes. Embracing changing conditions and acknowledging system limitations promotes safety.
New Age Motors: Your Brake Experts
So, at New Age Motors, we’ve mastered brake maintenance and repair services. We design our premier products exclusively around the needs of heavy truck fleets. We never lose sight of quality, safety or customer satisfaction. This promise is the reason why we’re your trusted partner in keeping your fleet on the road.
Expertise in Heavy-Duty Maintenance
With years of specialized knowledge in heavy-duty brake systems, our technicians are equipped to diagnose and repair your vehicle’s brakes with pinpoint accuracy. Years of practical experience lets us diagnose brake problems quickly, keeping your shop downtime to a minimum.
From routine checks to full-scale system restorations, we handle it all. Our services include comprehensive brake inspections, pad replacements and rotor resurfacing, hydraulic and air brake system overhauls, and brake fluid flushing and replacement.
This wide range guarantees the reliability of your truck’s braking system even in the most grueling and severe conditions, minimizing risk and boosting performance.
Advanced Diagnostic Capabilities
We use cutting-edge diagnostic technology to evaluate brake performance with pinpoint precision. By using new digital technologies to identify problems early, you can avoid expensive repairs or long vehicle downtime.
Catching wear or malfunctions before they become issues increases your safety. The repair goes a long way toward increasing the life of your entire braking system. When you trust professional diagnostics, you don’t just improve your bottom line—you get peace of mind for every mile your truck rolls.
Customer-Focused Service Approach
Our service philosophy is all about you. Our culture of open communication and transparency informs every interaction we have, from addressing your repair needs to offering fair, upfront pricing before beginning any work.
Your feedback is important to us, and we’re using it to improve our services. Your safety, comfort and enjoyment will continue to be our guiding principles, backed by our long-standing partnership with OTR Fleet Service.
Conclusion
Keeping heavy truck brakes in optimum condition is vital for keeping our roadways safe. This task is more than maintenance—it’s maintenance plus an absolute first line of defense. Good, strong brakes ensure you maintain control of your vehicle, while preventing harm to those around you and minimizing expensive, unpredictable downtime. Consistent maintenance, strong driver practices, and the adoption of advanced safety technologies help save lives. Every step increases the performance and dependability of your truck.
At New Age Motors, we understand heavy truck brakes better than anyone else. From preventative maintenance inspections to enforcement upgrades, we are ready to help you build positive momentum. Stop waiting for a brake problem to rear its ugly head– allow us to keep your heavy truck fleet running safely and efficiently. Write or call to us today and find out how we can help you grow and succeed on your path. A world with safe roads begins with making better, smarter decisions.
Frequently Asked Questions
What makes heavy truck brakes different from regular vehicle brakes?
Heavy truck brakes are designed for the increased weight and stress. This is because they tend to use air brake systems, which are favored for reliability and performance, unlike hydraulic brakes in light vehicles.
How often should heavy truck brakes be inspected?
Inspect heavy truck brakes at least every 5,000 or 8,000 kilometers, or at each piece of equipment’s preventive maintenance service interval. Proactive inspection and maintenance will improve safety and help avoid expensive breakdowns.
What are common signs of heavy truck brake problems?
Listen for squeaking sounds, feel for a loss of braking ability, vibration in the pedal, or an air pressure drop. These signals are warning you of underlying problems that require immediate action.
Why do heavy truck brakes wear out faster?
Heavy loads, frequent braking, steep terrain all contribute to quick brake wear. With proper maintenance and adoption of safer driving practices, heavy truck brake life can be significantly improved.
Can advanced technologies improve brake safety?
Inclusion of features such as ABS (anti-lock braking systems) are tremendously effective advanced safety features. They help eliminate skids and increase vehicle control in emergency situations.
How does driver training impact brake performance?
Proper driver training leads to appropriate brake use, saving wear and improving safety. Experienced operators understand when to downshift and minimize hard braking.
Why choose New Age Motors for brake services?
New Age Motors knows heavy truck brakes and that’s why we employ highly skilled technicians, use high quality parts, and provide courteous and dependable service. With our help, you can be sure that your heavy truck brakes are both safe and efficient.
Explore The Full Range of Services Offered By New Age Motors:
Read Further on Vehicle Safety and Standards
Alberta Motor Vehicle Industry Council